Guide complet des matériaux pour outils de coupe en usinage : Tendances et technologies
12/12/2023
Dans un monde industriel en constante évolution, les outils de coupe en usinage jouent un rôle crucial, avec un marché mondial estimé à plusieurs milliards de dollars. Mais comment choisir parmi la vaste gamme de matériaux disponibles ? Aciers rapides, carbures métalliques, céramiques… chaque matériau offre des avantages spécifiques, adaptés à diverses applications.
Ce guide complet explore les dernières tendances et technologies, dévoilant comment ces matériaux révolutionnent l’efficacité et la précision en usinage. Êtes-vous prêts à plonger dans l’univers fascinant des matériaux pour outils de coupe ? Découvrons ensemble ce que l’avenir nous réserve.
1. Les aciers rapides (HSS)
1.1. Définition et utilisation générale
Les aciers rapides, connus sous l’acronyme HSS (High Speed Steel), sont des alliages spécialement conçus pour l’usinage à haute vitesse. Reconnus pour leur dureté exceptionnelle et leur résistance à la déformation sous des températures élevées, ces aciers sont indispensables dans les industries modernes pour leur efficacité et leur polyvalence.
Types d’aciers rapides et leurs spécificités
- HSS : La forme standard, idéale pour l’usinage manuel et des matériaux plus tendres.
- HSS-E (5% de cobalt) : Améliore la résistance à la chaleur, parfait pour les aciers inoxydables.
- HSSCo8 (8% de cobalt) : Accroît la vitesse de coupe, utilisé pour les aciers durs et les alliages de titane.
- HSS-V (au vanadium) : Excellente résistance à l’usure, adapté pour les matériaux générant de longs copeaux.
- HSS-PM (élaboré par métallurgie des poudres) : Offre une durée de vie prolongée, idéal pour l’usinage à sec de matériaux difficiles comme le nickel ou le titane.
Comme vous venez de le lire le Vanadium (VA) et le Cobalt (CO) entrent dans la composition des aciers rapides et ils ont donné l’acronyme VACO, raison sociale de notre société.
1.2. Applications pratiques
Ces aciers trouvent leur place dans la fabrication d’une multitude d’outils coupants : forets, tarauds, fraises, et bien d’autres. Leur capacité à maintenir une dureté élevée même sous des températures extrêmes les rend essentiels pour les opérations d’usinage exigeantes, garantissant précision et qualité dans la production industrielle.
2. Autres matériaux utilisés dans les outils coupants
2.1. Aciers au carbone
Les aciers au carbone, avec leur teneur typique de 0,8 à 1,05 % en carbone, offrent une solution économique pour des travaux de coupe à faible vitesse. Principalement utilisés pour des opérations de finition, ils combinent coût abordable et performance adéquate dans des conditions de coupe moins exigeantes.
2.2. Carbures métalliques
Constitués principalement de carbure de tungstène, ces matériaux offrent une dureté et une résistance à l’usure exceptionnelles. Ils sont idéaux pour les opérations d’usinage à haute vitesse, notamment sur des matériaux durs comme les aciers trempés et les fontes.
2.3. Céramiques
Les céramiques, frittées à partir d’oxyde d’alumine, se distinguent par leur grande dureté et leur résistance à l’usure à haute température. Elles conviennent particulièrement à l’usinage de métaux ferreux à des vitesses de coupe élevées, bien qu’elles soient sensibles aux chocs.
2.4. Diamants industriels
Les diamants industriels, extrêmement durs, sont utilisés pour le travail des métaux non ferreux et certains matériaux non métalliques. Ils offrent une excellente finition de surface, notamment dans l’usinage de matériaux comme l’aluminium ou le graphite.
2.5. Cermets
Les cermets, alliant titane et liants comme le nickel ou le cobalt, se spécialisent dans les opérations de finition. Ils présentent une résistance à l’usure et une stabilité chimique remarquables, particulièrement adaptées au tournage de finition des aciers inoxydables.
2.6. Nitrure de bore cubique (CBN)
Le CBN, l’un des matériaux de coupe les plus durs, est privilégié pour la finition de matériaux très durs comme les aciers trempés. Sa grande dureté et résistance à l’usure le rendent indispensable pour les applications exigeant une grande précision et une durée de vie élevée de l’outil.
3. Revêtements et traitements des outils coupants
3.1. Importance des revêtements
Les revêtements sur les outils coupants ne sont pas seulement une question d’esthétique ; ils sont cruciaux pour améliorer la performance et la durée de vie des outils. En fournissant une couche supplémentaire de protection, ces revêtements réduisent l’usure, minimisent le frottement et améliorent la résistance à la chaleur.
3.2. Types de revêtements
TiN (Nitrure de Titane) : revêtement couramment utilisé dans diverses applications en raison de ses excellentes propriétés tribologiques (résistance à l’usure et au frottement) et de sa résistance à la corrosion.
Dureté : le TiN est connu pour sa dureté élevée, généralement dans la plage de 2000 à 2500 Vickers, ce qui le rend résistant à l’abrasion et à l’usure.
Adhérence : le revêtement TiN a généralement une bonne adhérence à différents substrats métalliques, ce qui garantit une longue durée de vie du revêtement.
Épaisseur du revêtement : l’épaisseur du revêtement TiN peut varier en fonction de l’application spécifique. En général, elle se situe entre 1 et 5 micromètres.
Couleur : le TiN a une couleur dorée caractéristique, ce qui lui donne également un aspect esthétique.
Coefficient de frottement : le TiN réduit le coefficient de frottement, ce qui améliore les propriétés tribologiques des pièces revêtues.
Résistance à la corrosion : le TiN offre une bonne résistance à la corrosion, ce qui le rend adapté à des environnements agressifs.
Température de fonctionnement : le TiN peut généralement résister à des températures relativement élevées, ce qui le rend adapté à des applications où des températures élevées peuvent être rencontrées.
Applications : le TiN est couramment utilisé comme revêtement pour des outils de coupe (forets, tarauds, fraises, plaquettes ,…)
TiCN (Carbonitrure de Titane) : revêtement utilisé dans l’industrie des outils de coupe nécessitant une résistance à l’usure et à la chaleur. Le TiCN est composé principalement de titane (Ti), de carbone (C) et d’azote (N).
Dureté : le TiCN offre une dureté élevée, généralement dans la plage de 2 500 à 3 500 HV (dureté Vickers). Cette dureté élevée confère au revêtement une résistance supérieure à l’usure.
Adhérence : le TiCN a généralement une bonne adhérence aux substrats métalliques, ce qui est essentiel pour assurer la durabilité du revêtement.
Coefficient de frottement : le TiCN a généralement un coefficient de frottement assez faible, ce qui contribue à réduire l’usure pendant les opérations de coupe et à améliorer la durée de vie de l’outil.
Température de fonctionnement : le TiCN offre une stabilité thermique élevée, ce qui signifie qu’il peut résister à des températures élevées sans dégradation significative de ses propriétés.
Couleur : le TiCN a souvent une couleur violette à bronze, ce qui peut être utile pour l’identification visuelle sur les outils.
Applications : le revêtement TiCN est largement utilisé dans l’industrie des outils de coupe (forets, fraises, tarauds, plaquettes,..).
TiAlN (nitrure de titane et aluminium) : revêtement dur et résistant utilisé dans diverses applications industrielles, notamment dans l’outillage, la coupe des métaux et d’autres applications de revêtement pour améliorer la résistance à l’usure et prolonger la durée de vie des outils.
Le revêtement TiAlN est composé de nitrure de titane (TiN) et de nitrure d’aluminium (AlN). La combinaison de ces deux éléments confère au revêtement des propriétés améliorées en termes de dureté et de résistance à l’usure.
Dureté : a plage de dureté typique pour le TiAlN se situe généralement entre 2 000 et 3 500 HV,
Coefficient de frottement : le revêtement TiAlN a généralement un faible coefficient de frottement, ce qui réduit la friction entre l’outil revêtu et le matériau traité. Cela contribue à améliorer l’efficacité de la coupe et à prolonger la durée de vie de l’outil.
Température de fonctionnement :
Le TiAlN est capable de résister à des températures élevées, ce qui en fait un choix populaire pour les applications à haute température, telles que l’usinage à grande vitesse.
Adhérence et cohésion : un bon revêtement doit adhérer solidement à la surface de l’outil de base et doit également avoir une cohésion interne élevée pour résister aux contraintes mécaniques.
Couleur : le TiAlN a souvent une couleur dorée à bronze, bien que la teinte puisse varier en fonction des conditions de dépôt et de la composition exacte du revêtement.
Applications : le revêtement TiAlN est largement utilisé dans l’industrie de l’usinage pour les outils de coupe, les forets, les fraises, etc. Il est également utilisé dans d’autres applications nécessitant une résistance à l’usure et à la corrosion.
AlTiN (nitrure d’aluminium et titane) : revêtement composite utilisé principalement dans l’industrie de l’outillage et de l’usinage pour améliorer les propriétés de surface des outils de coupe
Principalement composé d’aluminium (Al), de titane (Ti) et d’azote (N).
Dureté : l’AlTiN offre une dureté élevée, ce qui contribue à prolonger la durée de vie des outils de coupe.
Coefficient de frottement : faible coefficient de frottement, ce qui améliore l’efficacité de coupe.
Résistance à l’usure : excellente résistance à l’usure, permettant une durée de vie prolongée des outils et une meilleure performance dans des conditions d’usinage difficiles.
Résistance à la chaleur : bonne résistance à la chaleur, ce qui permet une utilisation à des températures élevées sans perte significative de performance.
Adhérence : une adhérence élevée au substrat de l’outil, assurant une durabilité prolongée.
Couleur : généralement, l’AlTiN a une couleur violet-noir.
Applications : utilisé principalement pour les outils de coupe dans l’usinage à grande vitesse (HSM) de métaux et autres matériaux durs.
Revêtement PVD (dépôt physique en phase vapeur) : l’AlTiN est souvent déposé sur les outils par la technique de dépôt PVD, qui donne une couche fine mais robuste.
Épaisseur du revêtement : l’épaisseur du revêtement AlTiN peut varier en fonction de l’application spécifique et des exigences de l’outil.
ZrN (nitrure de zirconium) : revêtement souvent utilisé l’usinage des métaux non ferreux, alliages d’aluminium,..
Dureté : le ZrN est connu pour sa dureté élevée, ce qui en fait un revêtement robuste et résistant à l’usure. La dureté du revêtement ZrN se situe dans une plage d’environ 2000 à 3000 HV.
Adhérence : il a généralement une bonne adhérence à la plupart des substrats métalliques, assurant ainsi une liaison solide entre le revêtement et le matériau de base.
Coefficient de frottement : le ZrN a un faible coefficient de frottement, ce qui améliore la lubrification et réduit l’usure dans les applications tribologiques.
Résistance à l’usure : en raison de sa dureté, le ZrN offre une excellente résistance à l’usure, ce qui le rend approprié pour les applications où une protection contre l’abrasion est nécessaire.
Résistance à la corrosion : le nitrure de zirconium est généralement résistant à la corrosion, ce qui améliore la durabilité du matériau de base contre les environnements agressifs.
Température de fonctionnement : le ZrN peut généralement fonctionner à des températures élevées sans perdre ses propriétés, ce qui le rend adapté aux applications à haute température.
Couleur : le ZrN a une couleur dorée, ce qui peut également être esthétiquement attrayant dans certaines applications.
AlCrN (aluminium chrome nitride) : revêtement de surface utilisé principalement dans l’industrie de l’usinage et de l’outillage pour améliorer les propriétés des outils de coupe, des forets, des fraises, etc.
Dureté : l’AlCrN est connu pour sa dureté élevée, ce qui améliore la résistance à l’usure des outils revêtus. La dureté élevée permet aux outils de maintenir leur tranchant plus longtemps, prolongeant ainsi leur durée de vie.
Résistance à l’usure : ce revêtement offre une excellente résistance à l’usure, ce qui le rend adapté aux environnements d’usinage difficiles où les outils sont soumis à des charges élevées et à des températures élevées.
Résistance à la chaleur : l’AlCrN a une bonne résistance à la chaleur, ce qui le rend approprié pour les applications à haute température, telles que l’usinage à grande vitesse.
Coefficient de frottement réduit : il a un faible coefficient de frottement, ce qui contribue à réduire la chaleur générée pendant l’usinage et à améliorer les performances globales de l’outil.
Adhérence : le revêtement AlCrN a généralement une bonne adhérence à la surface de l’outil, assurant une protection durable.
Compatibilité avec divers matériaux : il est utilisé pour l’usinage d’une variété de matériaux, y compris les aciers, les alliages d’aluminium, les aciers inoxydables, etc.
Couleur : l’AlCrN a souvent une couleur dorée ou bronze caractéristique.
Épaisseur du revêtement : la plage d’épaisseur du revêtement AlCrN peut varier en fonction des spécifications du fabricant et de l’application spécifique.
Vapeur : traitement de surface vaporisé surtout utilisé en taraudage qui améliore le coulissement du taraud. Il peut être couplé avec un traitement de nitruration qui augmente la dureté de de surface ainsi qu’une amélioration des propriétés de glissement particulièrement adapté pour les matériaux abrasifs (fonte grise, fonte d’aluminium à haute teneur en silice,…)
3.3. Impact sur la performance et la durabilité des outils
Ces revêtements transforment les outils coupants en véritables champions de l’endurance et de l’efficacité. Ils permettent une coupe plus nette, réduisent le besoin de remplacement fréquent et assurent une performance constante, même dans des conditions d’usinage intensives.
Explorez notre gamme complète d’outils professionnels. Téléchargez le catalogue VACO France dès maintenant et découvrez nos solutions sur mesure pour vos projets.
4. Tendances actuelles et innovations dans le domaine des outils coupants
4.1. Évolution des matériaux et techniques
L’industrie des outils coupants est témoin d’une évolution constante, avec l’émergence de nouveaux matériaux et techniques. L’intégration de technologies avancées, comme l’impression 3D et les nanotechnologies, ouvre des horizons prometteurs pour la création d’outils plus performants, précis et durables.
4.2. Focus sur la recherche et le développement
La recherche et le développement jouent un rôle clé dans le secteur des outils coupants. Les investissements croissants dans la R&D visent non seulement à améliorer les matériaux existants, mais également à découvrir de nouvelles compositions et revêtements, capables de répondre aux défis de l’usinage moderne.
Conclusion
Cet article a exploré l’univers diversifié et dynamique des matériaux pour outils de coupe en usinage, allant des aciers rapides aux innovations comme le nitrure de bore cubique et les diamants industriels. Les revêtements, tels que TiN et AlcrN, ont également été mis en lumière pour leur rôle crucial dans l’amélioration des performances des outils.
Avec les avancées continues en recherche et développement, l’avenir des outils coupants s’annonce riche en innovations. De nouveaux matériaux, techniques et revêtements émergeront, poussant toujours plus loin les limites de l’efficacité, de la précision et de la durabilité en usinage.
Autres articles
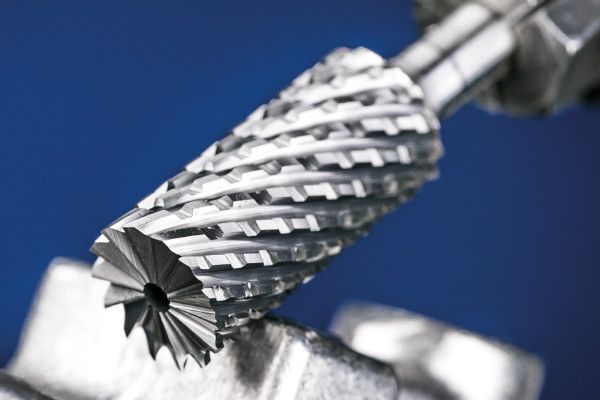
Fraises limes rotatives : le guide complet
01/12/2023
Cet article est votre guide complet pour comprendre et maîtriser ces outils indispensables. Vous êtes prêts à explorer en profondeur les caractéristiques, les utilisations et les avantages des fraises limes rotatives ? Suivez-nous dans ce voyage informatif.
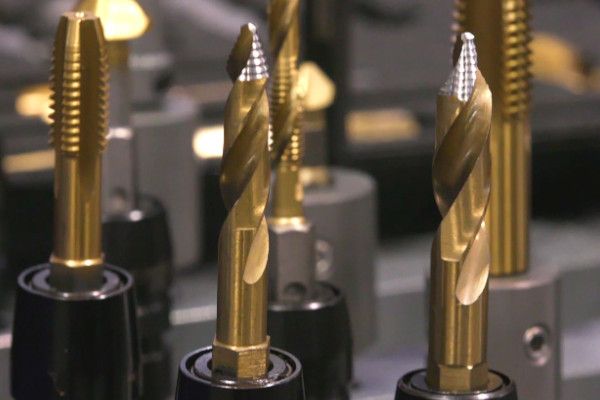
Les coûts cachés des outils coupants bon marché
22/12/2023
Explorer les coûts cachés, pourquoi choisir des outils de qualité supérieure, tels que VacoDrive®, représente une décision stratégiquement avantageuse pour les entreprises soucieuses de leur efficacité et de leur rentabilité.
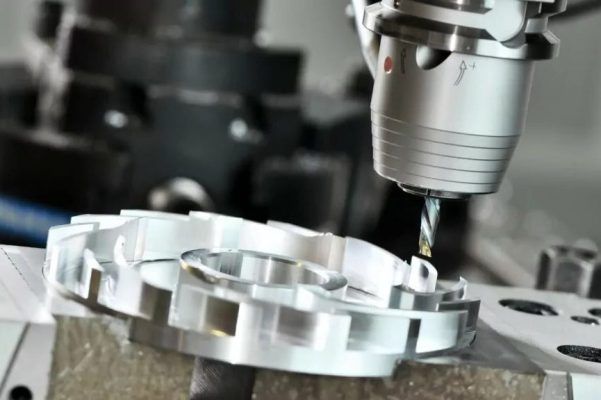
Usinage de l’inox : défis et solutions
18/01/2024
Découvrez dans cet article comment surmonter ces obstacles et exploiter au mieux les avantages de l'inox. Êtes-vous prêts à plonger dans le monde fascinant de l'usinage de l'inox ?